Creating a Welding WPS: Step-by-Step Directions for Professionals
Creating a Welding WPS: Step-by-Step Directions for Professionals
Blog Article
Opening the Power of Welding WPS: Strategies for Performance and Safety in Fabrication
In the world of manufacture, Welding Treatment Requirements (WPS) stand as the foundation of welding operations, dictating the necessary steps for attaining both performance and safety and security in the construction process. Comprehending the intricacies of WPS is vital to utilizing its full possibility, yet several companies have a hard time to unlock real power that lies within these records (welding WPS). By delving right into the techniques that maximize welding WPS, a world of improved productivity and increased safety awaits those happy to explore the subtleties of this essential element of fabrication

Value of Welding WPS
The significance of Welding Procedure Requirements (WPS) in the construction industry can not be overemphasized. WPS act as a vital roadmap that details the required actions to make sure welds are performed continually and properly. By defining necessary specifications such as welding procedures, products, joint layouts, preheat temperatures, interpass temperatures, filler steels, and post-weld warmth therapy demands, WPS give a standard approach to welding that enhances effectiveness, high quality, and security in manufacture procedures.
Adherence to WPS aids in achieving harmony in weld top quality, minimizing the probability of issues or architectural failings. This standardization additionally promotes conformity with sector regulations and codes, guaranteeing that fabricated structures fulfill the required security requirements. Furthermore, WPS documents enables welders to duplicate effective welding treatments, resulting in regular results across various projects.
In essence, the careful growth and strict adherence to Welding Procedure Specs are extremely important for upholding the integrity of welded frameworks, guarding versus potential risks, and maintaining the online reputation of manufacture business for delivering high-quality services and products.
Crucial Element of Welding WPS
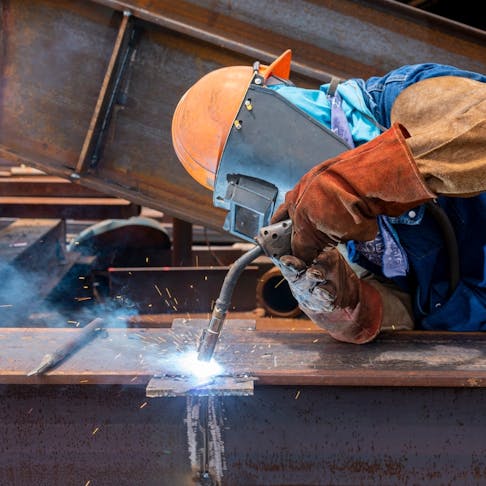
Enhancing Efficiency With WPS
When maximizing welding operations, leveraging the crucial elements described in Welding Treatment Specs (WPS) becomes crucial for making the most of and streamlining processes performance. One way to improve efficiency with WPS is by thoroughly picking this link the proper welding specifications. By sticking to the specific guidelines offered in the WPS, welders can guarantee that the welding equipment is established correctly, causing regular and high-grade welds. Furthermore, adhering to the pre-approved welding series described in the WPS can substantially minimize the moment invested in each weld, eventually enhancing overall productivity.
Furthermore, appropriate training and accreditation of welders in understanding and executing WPS can additionally enhance performance. Ensuring that all staff member are skilled in interpreting and carrying out the WPS accurately can more decrease mistakes and revamp, conserving both time and resources. On a regular basis evaluating and upgrading the WPS to incorporate any type of lessons found out or technological innovations can additionally add to efficiency improvements in welding procedures. By welcoming the guidelines established forth in the WPS and continuously looking for ways to enhance procedures, fabricators can accomplish greater efficiency levels and premium outcome.
Ensuring Safety in Fabrication
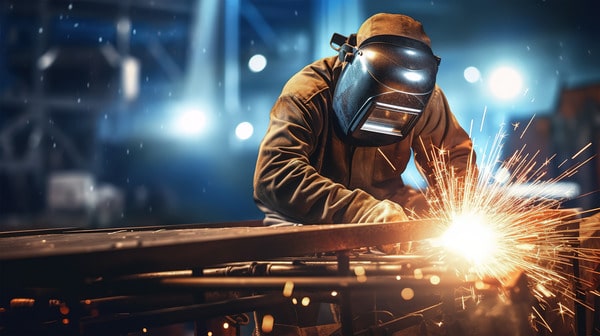
Ensuring safety and security in fabrication entails a diverse strategy that includes various elements of the welding procedure. Welders need to be equipped with proper gear such as helmets, handwear covers, and protective garments to mitigate threats associated with welding tasks.
Moreover, adherence to appropriate air flow and fume extraction systems is critical in maintaining a healthy and balanced workplace. Welding fumes have damaging materials that, if inhaled, can present serious health and wellness threats. Implementing efficient air flow measures assists to decrease exposure to these dangerous fumes, promoting breathing health amongst employees.
Regular devices upkeep and inspections are also necessary for ensuring safety in construction. Malfunctioning reference equipment can lead to injuries and mishaps, highlighting the significance of routine checks and timely repair services. By prioritizing security procedures and cultivating a culture of understanding, manufacture centers can develop a secure and productive workplace for their workers.
Implementing WPS Ideal Practices
To improve operational effectiveness and make sure top quality results in manufacture processes, including Welding Procedure Spec (WPS) ideal methods is critical. Selecting the proper welding process, filler product, and preheat temperature level defined in the WPS is important for attaining the desired weld high quality. Guaranteeing that certified welders with the necessary accreditations carry out the welding treatments according to the WPS guidelines is crucial for uniformity and integrity.
Conclusion
In conclusion, welding WPS plays an essential function in making sure performance and safety and security in fabrication processes. By following these methods, services can open the complete capacity of welding WPS in their construction operations.
In the realm of fabrication, Welding Procedure Specs (WPS) stand as the foundation of welding operations, dictating the necessary steps for accomplishing both efficiency and security in the construction process. By defining vital specifications such as welding procedures, products, joint layouts, preheat temperature levels, interpass temperature levels, filler metals, and post-weld warmth treatment demands, WPS offer a standardized approach to welding that enhances efficiency, quality, and safety and security in manufacture processes.
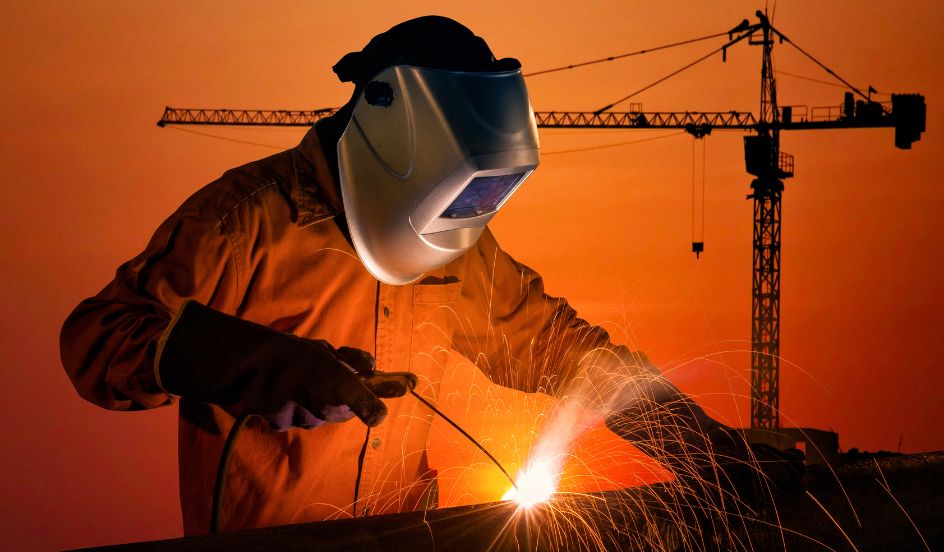
When maximizing welding operations, leveraging the essential aspects laid out in Welding Procedure Specs (WPS) comes to be important for enhancing procedures and making the most of efficiency. (welding WPS)
Report this page